Crafting a Metal Coat is a process that involves using specific materials and techniques to create a protective or decorative coating on a metal surface. This process can enhance the durability, appearance, and functionality of the metal object.
Metal coatings have been used for centuries to protect metal surfaces from corrosion, wear, and other environmental factors. They can also be used to improve the electrical conductivity, thermal properties, and appearance of metal objects. Modern metal coating techniques include electroplating, anodizing, powder coating, and thermal spraying.
The specific materials and techniques used to craft a metal coat will vary depending on the desired outcome. For example, electroplating is a process that uses an electric current to deposit a thin layer of metal onto a conductive surface. Anodizing is a process that creates a protective oxide layer on the surface of aluminum. Powder coating is a process that applies a dry powder coating to a metal surface, which is then cured using heat. Thermal spraying is a process that sprays molten metal onto a surface, which then solidifies to form a coating.
Can You Craft a Metal Coat?
Crafting a metal coat involves several key aspects, each contributing to the successful creation of a protective or decorative coating on a metal surface.
- Materials: The selection of appropriate materials, such as the type of metal and coating, is crucial for achieving the desired properties.
- Techniques: Various techniques, such as electroplating, anodizing, and powder coating, are employed to apply the coating effectively.
- Surface preparation: Proper preparation of the metal surface, including cleaning and pretreatment, ensures a strong bond between the coating and the metal.
- Coating thickness: Controlling the thickness of the coating is essential for optimizing its performance and durability.
- Curing: Some coating processes require a curing step to enhance the coating’s properties and ensure its longevity.
- Quality control: Implementing quality control measures is vital to ensure the coating meets the desired specifications.
- Safety precautions: Adhering to safety protocols is paramount when working with potentially hazardous materials and processes.
- Environmental considerations: Choosing environmentally friendly materials and processes is important for minimizing the impact on the environment.
Understanding these key aspects is essential for successfully crafting a metal coat. By carefully considering the materials, techniques, and other factors involved, you can achieve a high-quality coating that meets your specific requirements.
Materials
When crafting a metal coat, selecting the appropriate materials is paramount to achieving the desired properties, such as durability, corrosion resistance, and appearance. The type of metal and coating used will significantly impact the outcome, and careful consideration must be given to their compatibility and the specific requirements of the application.
- Metal selection: The type of metal used for the base material and the coating will influence the overall properties of the metal coat. Factors to consider include strength, weight, corrosion resistance, and thermal conductivity. Common metals used for metal coating include steel, aluminum, and copper.
- Coating selection: The choice of coating material depends on the desired properties and the application environment. Common coating materials include zinc, chromium, nickel, and various polymers. Each material offers unique characteristics, such as enhanced corrosion protection, improved wear resistance, or decorative finishes.
- Compatibility: Ensuring compatibility between the metal and the coating is crucial for a successful metal coat. Some coating materials may not adhere well to certain metals, leading to premature failure. Proper research and testing are essential to determine the compatibility of the chosen materials.
Understanding the connection between materials and the properties of a metal coat is vital for achieving optimal performance. By carefully selecting the appropriate materials and considering their compatibility, you can create a metal coat that meets your specific requirements and provides long-lasting protection and functionality.
Techniques
The choice of technique used to apply a metal coat significantly impacts the properties and characteristics of the final product. Different techniques offer unique advantages and are suited to specific applications.
- Electroplating involves passing an electric current through a solution containing metal ions, causing the metal to deposit on the surface of the base material. This technique provides a thin, uniform coating that enhances corrosion resistance and electrical conductivity.
- Anodizing is an electrochemical process that creates a protective oxide layer on the surface of metals, typically aluminum. This coating enhances corrosion resistance, wear resistance, and can also be used for decorative purposes.
- Powder coating involves applying dry powder particles to the metal surface, which are then melted and fused to form a durable coating. This technique provides a wide range of color and texture options, along with excellent resistance to corrosion and wear.
Selecting the appropriate technique depends on factors such as the desired properties of the coating, the type of metal being coated, and the intended application. By understanding the capabilities and limitations of each technique, you can craft a metal coat that meets your specific requirements and provides long-lasting performance.
Surface preparation
Surface preparation is a crucial step in the process of crafting a metal coat, as it directly influences the adhesion and durability of the coating. By properly preparing the metal surface, you create a clean and receptive surface that promotes a strong bond between the coating and the metal. This strong bond is essential for ensuring the long-term performance and effectiveness of the metal coat.
The process of surface preparation typically involves cleaning the metal surface to remove any dirt, oil, or other contaminants that could interfere with the bonding process. This can be done using a variety of methods, such as solvent cleaning, degreasing, or abrasive blasting. Once the surface is clean, it may also undergo pretreatment, such as phosphating or chromating, to further enhance the bond between the coating and the metal.
Understanding the importance of surface preparation and implementing proper techniques is essential for crafting a metal coat that meets your specific requirements. By ensuring a strong bond between the coating and the metal, you can create a durable and long-lasting finish that will protect and enhance the metal substrate.
Coating thickness
Controlling the thickness of the coating is a critical aspect of crafting a metal coat, as it directly influences the performance and durability of the final product. The thickness of the coating affects various properties, including corrosion resistance, wear resistance, and electrical conductivity.
A thicker coating generally provides better protection against corrosion and wear. However, it is important to consider the specific application and requirements when determining the optimal coating thickness. For example, a thicker coating may be necessary for applications where the metal will be exposed to harsh environmental conditions or heavy wear. Conversely, a thinner coating may be sufficient for applications where weight or electrical conductivity are important considerations.
Understanding the relationship between coating thickness and performance is essential for crafting a metal coat that meets specific requirements. By carefully controlling the coating thickness, you can optimize the performance and durability of the metal coat, ensuring that it provides the desired level of protection and functionality.
Curing
In the context of crafting a metal coat, curing is a crucial step that significantly impacts the performance and durability of the final product. Curing involves subjecting the coated metal to specific conditions, such as heat or ultraviolet light, to promote cross-linking and polymerization within the coating material.
- Enhanced Coating Properties: Curing enhances the mechanical properties of the coating, improving its hardness, adhesion, and resistance to wear and tear. This results in a more durable and long-lasting metal coat that can withstand harsh operating conditions.
- Improved Corrosion Resistance: Proper curing promotes the formation of a dense and uniform coating that effectively protects the metal substrate from corrosion. By preventing the penetration of corrosive substances, curing ensures the longevity of the metal coat and the underlying metal.
- Optimized Electrical Conductivity: For metal coats intended for electrical applications, curing plays a vital role in optimizing electrical conductivity. It enhances the electrical properties of the coating, reducing resistance and ensuring efficient current flow.
- Increased Chemical Resistance: Curing improves the chemical resistance of the coating, making it less susceptible to degradation by acids, alkalis, and other chemicals. This is particularly important for metal coats exposed to harsh chemical environments.
Understanding the importance of curing and implementing proper curing techniques are essential for crafting high-quality metal coats that meet specific performance requirements. By carefully controlling the curing process, you can enhance the properties of the coating, ensuring its long-term effectiveness and durability.
Quality Control
Quality control is an indispensable aspect of crafting a metal coat that meets the desired specifications and performs as intended. Implementing rigorous quality control measures throughout the coating process ensures that the final product aligns with the established standards and requirements.
- Inspection and Testing: Regular inspection and testing of the coating at various stages of the process help identify any deviations from the desired specifications. This involves using specialized equipment and techniques to evaluate the coating’s thickness, adhesion, corrosion resistance, and other critical properties.
- Process Control: Establishing and adhering to standardized coating processes is essential for maintaining consistent quality. This includes controlling factors such as the preparation of the metal surface, the application of the coating material, and the curing conditions. By minimizing variability in the process, manufacturers can reduce the likelihood of defects and ensure the desired coating properties.
- Material Certification: Utilizing certified coating materials and adhering to the manufacturer’s specifications is crucial for achieving the desired coating performance. This involves verifying the quality and composition of the coating materials and ensuring their compatibility with the metal substrate and the intended application.
- Documentation and Traceability: Maintaining proper documentation and traceability throughout the coating process is essential for quality control. This includes recording the coating parameters, inspection results, and any corrective actions taken. This documentation serves as a valuable reference for future analysis and improvement.
By implementing these quality control measures, manufacturers can ensure that the crafted metal coat meets the desired specifications, resulting in a high-performing and durable product that meets the intended application requirements.
Safety precautions
Crafting a metal coat involves working with potentially hazardous materials and processes, making adherence to safety protocols paramount. Understanding and implementing these precautions is crucial to prevent accidents, protect health, and ensure the safe handling of hazardous substances.
For instance, electroplating, a common technique in metal coating, utilizes electrolytes and chemical solutions that can pose risks such as skin irritation, respiratory problems, and chemical burns. Anodizing, another technique, involves the use of acids and high voltages, presenting electrical hazards and the potential for chemical exposure. By adhering to safety protocols, such as wearing appropriate protective gear, ensuring proper ventilation, and following established procedures, individuals can minimize these risks and work safely.
Moreover, safety precautions extend beyond the coating process itself. Proper storage and disposal of hazardous materials are essential to prevent environmental contamination and protect public health. Following established guidelines and regulations ensures that these materials are handled responsibly throughout their lifecycle.
In conclusion, safety precautions are an indispensable component of crafting a metal coat. By recognizing the potential hazards associated with the materials and processes involved, individuals can prioritize safety, protect themselves and others, and contribute to a safe working environment.
Environmental considerations
In the context of crafting a metal coat, environmental considerations play a crucial role in minimizing the ecological impact of the process and the end product. Selecting environmentally friendly materials and processes involves carefully assessing the potential environmental implications at every stage, fromto.
One key aspect is choosing coating materials with low or noVOCs (volatile organic compounds). VOCs contribute to air pollution and can have adverse effects on human health and the environment. Water-based coatings, powder coatings, and high-solids coatings are examples of environmentally friendly alternatives that emit fewer VOCs.
Furthermore, selecting sustainable metal substrates is essential. Recycled metals have a lower environmental impact than those extracted from virgin ores. Using recycled metals reduces energy consumption, conserves natural resources, and minimizes waste.
Additionally, optimizing the coating process itself can reduce environmental impact. Proper surface preparation techniques minimize the need for harsh chemicals, and efficient application methods reduce waste and energy consumption. Implementing closed-loop systems for water and chemical recycling further enhances environmental sustainability.
By prioritizing environmental considerations in crafting a metal coat, manufacturers can contribute to a more sustainable and eco-conscious industry. It is not just about meeting regulatory requirements but also about demonstrating a commitment to environmental stewardship and reducing the ecological footprint of metal coating processes.
Frequently Asked Questions on Crafting a Metal Coat
This section addresses common questions and misconceptions surrounding the process of crafting a metal coat. It provides informative answers to guide readers in making informed decisions about their metal coating projects.
Question 1: What factors influence the choice of coating material?
The selection of coating material depends on numerous factors, including the desired properties, the application environment, and the compatibility with the metal substrate. Different materials offer unique advantages, such as enhanced corrosion resistance, improved wear resistance, or decorative finishes.
Question 2: How does surface preparation affect the coating’s performance?
Proper surface preparation is crucial for ensuring a strong bond between the coating and the metal. It involves cleaning the metal surface to remove contaminants and applying pretreatments to enhance adhesion. Inadequate surface preparation can compromise the coating’s performance and durability.
Question 3: What is the importance of controlling coating thickness?
Coating thickness plays a significant role in optimizing the coating’s performance. A thicker coating generally provides better protection against corrosion and wear, but it may impact other properties like electrical conductivity or weight. Determining the optimal coating thickness is essential for meeting specific application requirements.
Question 4: Why is curing necessary for certain coating processes?
Curing enhances the coating’s properties by promoting cross-linking and polymerization within the coating material. It improves the coating’s hardness, adhesion, and resistance to wear and tear. Proper curing is essential for achieving the desired performance and longevity of the metal coat.
Question 5: How can quality control ensure the coating meets specifications?
Implementing quality control measures throughout the coating process is crucial for ensuring that the final product meets the desired specifications. This involves regular inspection, testing, and adherence to standardized processes. Quality control helps identify and correct any deviations, resulting in a high-performing and durable metal coat.
Question 6: What environmental considerations should be taken into account when crafting a metal coat?
Environmental considerations involve selecting environmentally friendly materials and processes to minimize the ecological impact. This includes choosing low-VOC coatings, using recycled metals, and optimizing the coating process to reduce waste and energy consumption. Prioritizing environmental sustainability helps reduce the ecological footprint of metal coating.
These FAQs provide a comprehensive overview of the key aspects to consider when crafting a metal coat. Understanding these factors enables individuals to make informed decisions, achieve the desired performance, and contribute to environmental sustainability in their metal coating projects.
To learn more about specific techniques and applications of metal coating, please refer to the relevant sections of this comprehensive guide.
Tips for Crafting a Metal Coat
Crafting a metal coat involves various techniques and considerations. Here are some valuable tips to ensure a successful and effective metal coating process:
Tip 1: Material Selection: Choosing the appropriate metal and coating materials is crucial. Consider the desired properties, such as corrosion resistance, wear resistance, and electrical conductivity. Ensure compatibility between the metal substrate and the coating material to achieve optimal adhesion and performance.
Tip 2: Surface Preparation: Proper surface preparation before coating is essential. Remove contaminants, oils, and oxides from the metal surface to create a clean and receptive surface. This promotes strong adhesion between the coating and the metal, enhancing the overall durability of the metal coat.
Tip 3: Coating Thickness Control: Determine the optimal coating thickness based on the application requirements. A thicker coating provides better protection against corrosion and wear, but it may affect other properties like electrical conductivity or weight. Optimize the coating thickness to achieve the desired performance and functionality.
Tip 4: Proper Curing: If required by the coating process, follow the recommended curing procedures. Curing enhances the coating’s properties by promoting cross-linking and polymerization, resulting in improved hardness, adhesion, and resistance to wear and tear. Proper curing ensures the long-term durability and effectiveness of the metal coat.
Tip 5: Quality Control: Implement quality control measures throughout the coating process to ensure the final product meets the desired specifications. Conduct regular inspections, tests, and adherence to standardized processes. This helps identify and correct any deviations, resulting in a high-performing and consistent metal coat.
Tip 6: Environmental Considerations: Choose environmentally friendly materials and processes when crafting a metal coat. Use low-VOC coatings, recycled metals, and optimize the coating process to reduce waste and energy consumption. Prioritizing environmental sustainability minimizes the ecological impact of metal coating.
These tips provide guidance for crafting a metal coat that meets specific requirements and performs effectively. By considering these factors, individuals can achieve successful metal coating outcomes.
For more detailed information on metal coating techniques and applications, refer to the relevant sections of this comprehensive guide.
Conclusion
Crafting a metal coat involves a comprehensive process that encompasses selecting appropriate materials, employing suitable techniques, and adhering to quality standards. This article has explored the various aspects of metal coating, highlighting the significance of each step in achieving the desired properties and performance.
Understanding the principles and best practices of metal coating empowers individuals to make informed decisions and achieve successful outcomes in their metal coating projects. By considering factors such as material compatibility, surface preparation, coating thickness, curing, quality control, and environmental impact, crafters can create metal coats that meet specific requirements and provide long-lasting protection and functionality.
Youtube Video:
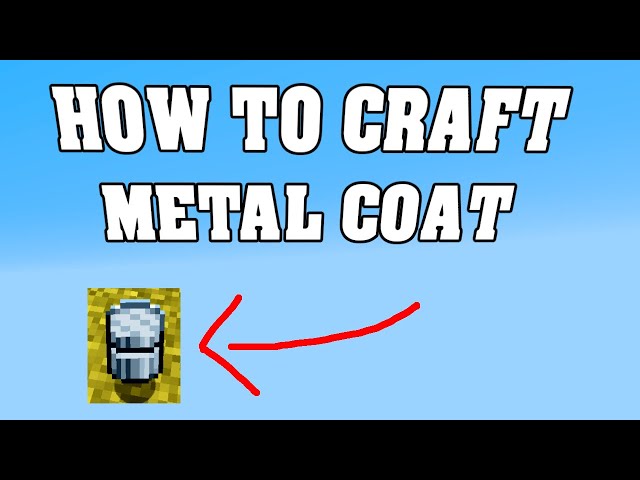