A piston crafting recipe is a set of instructions detailing the materials and steps required to create a piston, a crucial component in many mechanical systems, particularly engines. It involves selecting the appropriate materials, shaping them precisely, and assembling them correctly to ensure the piston’s functionality and durability.
Crafting a piston requires precision and adherence to specifications to achieve the desired performance and efficiency. The choice of materials, such as aluminum alloys or steel, depends on factors like the engine’s operating conditions and power requirements. The recipe includes instructions for machining the piston’s shape, including its crown, ring grooves, and, to ensure proper fit and movement within the engine’s cylinder.
The main article will delve into the specifics of piston crafting recipes, exploring material selection, machining processes, and quality control measures. It will also highlight the importance of these recipes in ensuring the reliability and performance of engines across various applications, from automotive to industrial settings.
Piston Crafting Recipe
Crafting a piston requires a precise recipe, a set of instructions that guides the selection of materials, machining processes, and assembly techniques. Six key aspects are crucial in this recipe:
- Material Selection: Choosing the right material, such as aluminum alloys or steel, is essential for durability and performance.
- Machining Accuracy: Precise machining ensures proper fit and movement within the engine’s cylinder.
- Crown Design: The shape of the piston’s crown affects combustion efficiency and engine power.
- Ring Groove Placement: Proper placement of ring grooves is critical for effective sealing and oil control.
- Surface Finish: A smooth surface finish reduces friction and wear, enhancing piston longevity.
- Quality Control: Rigorous quality control measures ensure that each piston meets the required specifications.
These aspects are interconnected and influence the overall performance and reliability of the engine. Material selection, for instance, impacts the piston’s weight, thermal conductivity, and resistance to wear. Machining accuracy affects the piston’s ability to withstand high pressures and temperatures. The crown design influences the engine’s combustion efficiency and power output. Ring groove placement affects oil consumption and blow-by. Surface finish reduces friction and wear, extending the piston’s lifespan. Quality control ensures that each piston meets the required specifications for optimal engine performance.
Material Selection
In the context of piston crafting, material selection plays a pivotal role in determining the durability and performance of the final product. The choice of material directly influences the piston’s ability to withstand the extreme conditions encountered within an engine, including high temperatures, pressures, and mechanical stresses.
- Strength and Durability: The material must possess sufficient strength to endure the high pressures and temperatures generated during combustion. Aluminum alloys and steel are commonly used due to their high strength-to-weight ratios and resistance to wear.
- Thermal Conductivity: Good thermal conductivity is crucial for efficient heat transfer away from the piston crown, preventing overheating and ensuring proper engine operation. Aluminum alloys excel in this aspect, facilitating effective heat dissipation.
- Weight and Friction: The material’s weight can affect engine performance and fuel efficiency. Lighter materials, such as aluminum alloys, reduce reciprocating mass, leading to improved acceleration and reduced fuel consumption. Additionally, a low coefficient of friction between the piston and cylinder bore minimizes energy losses due to friction.
- Cost and Availability: Material selection must also consider cost and availability. Aluminum alloys are relatively affordable and widely available, making them a practical choice for mass-produced engines. Steel, while offering superior strength, may be more expensive and require specialized manufacturing techniques.
The optimal material selection for a piston crafting recipe depends on the specific engine application and performance requirements. By carefully considering the factors discussed above, engineers can choose the most suitable material to ensure the piston’s durability, performance, and overall engine efficiency.
Machining Accuracy
In the context of piston crafting, machining accuracy is paramount for ensuring the piston’s proper fit and movement within the engine’s cylinder. Precise machining processes guarantee that the piston’s dimensions, shape, and surface finish meet the exacting specifications required for optimal engine performance and longevity.
The machining process involves shaping the piston from a raw material, typically a metal alloy such as aluminum or steel. Computer-controlled machines are employed to remove excess material and create the desired piston shape, including the piston’s crown, ring grooves, and skirt. Tight tolerances are maintained throughout the machining process to ensure that the piston conforms to the design specifications.
Precise machining is crucial for several reasons. First, it ensures a proper fit between the piston and the cylinder bore. This close fit minimizes blow-by, the leakage of combustion gases past the piston rings, which can reduce engine power and efficiency. Second, accurate machining ensures that the piston moves smoothly within the cylinder without excessive friction. This reduces wear and tear on the piston and cylinder bore, extending the engine’s lifespan. Third, precise machining helps to optimize the piston’s performance and efficiency. By maintaining the correct piston shape and surface finish, engineers can minimize heat transfer and maximize combustion efficiency, leading to improved engine power and fuel economy.
The importance of machining accuracy in piston crafting cannot be overstated. It is a critical component of the piston crafting recipe, ensuring that the final product meets the required specifications for fit, performance, and durability. Precise machining is a testament to the skill and expertise of engineers and machinists, and it plays a vital role in the overall performance and reliability of engines across various applications.
Crown Design
In the context of piston crafting, crown design plays a critical role in optimizing combustion efficiency and engine power output. The shape of the piston’s crown influences the air-fuel mixture’s movement, flame propagation, and heat transfer within the combustion chamber.
- Combustion Chamber Shape: The crown’s shape determines the shape of the combustion chamber, which affects the air-fuel mixture’s flow and turbulence. A well-designed combustion chamber promotes efficient mixing and complete combustion, leading to increased power output and reduced emissions.
- Compression Ratio: The crown’s shape also affects the engine’s compression ratio, which is the ratio of the cylinder’s volume at the bottom of the stroke to its volume at the top of the stroke. A higher compression ratio generally results in increased power and efficiency, but it also increases the engine’s susceptibility to knocking.
- Valve Pockets: Pistons in engines with overhead valves feature valve pockets in the crown to accommodate the valves’ movement. The shape and depth of these pockets affect the flow of the air-fuel mixture around the valves, influencing combustion efficiency and power output.
- Swirl and Tumble: The crown’s shape can be designed to induce swirl or tumble motion in the air-fuel mixture as it enters the combustion chamber. This motion enhances mixing and promotes more complete combustion, leading to improved power and fuel economy.
The design of the piston’s crown is a complex and intricate process that requires careful consideration of multiple factors, including the engine’s operating conditions, performance targets, and emission standards. By optimizing the crown’s shape, engineers can improve combustion efficiency, increase engine power, and reduce emissions, demonstrating the critical role of crown design in the overall piston crafting recipe.
Ring Groove Placement
In the context of piston crafting, ring groove placement plays a vital role in ensuring effective sealing and oil control within the engine’s combustion chamber. The piston rings, housed within these grooves, perform two primary functions:
- Combustion Sealing: The top ring acts as a primary seal, preventing the combustion gases from leaking past the piston into the crankcase. Proper placement of this groove is crucial to maintain a tight seal and minimize blow-by, which can lead to power loss and increased emissions.
- Oil Control: The lower rings serve as oil control rings, scraping excess oil from the cylinder walls as the piston moves. Precise placement of these grooves ensures optimal oil removal, preventing oil consumption and maintaining proper lubrication of the piston and cylinder.
The placement of the ring grooves is determined by several factors, including the engine’s operating conditions, piston design, and ring specifications. Engineers carefully calculate the depth and spacing of the grooves to ensure that the rings exert the appropriate pressure against the cylinder walls for effective sealing and oil control.
Proper ring groove placement contributes to improved engine performance, reduced emissions, and increased fuel efficiency. By optimizing the sealing and oil control functions of the piston rings, engineers can minimize blow-by, reduce friction, and maintain optimal engine operation.
Surface Finish
In the context of piston crafting, surface finish plays a critical role in reducing friction and wear, thereby enhancing the piston’s longevity and overall performance. The surface finish of the piston, particularly the piston skirt and ring lands, directly influences its interaction with the cylinder bore and piston rings.
A smooth surface finish reduces friction between the piston and cylinder bore, minimizing power loss and improving engine efficiency. It also reduces wear on both surfaces, extending the lifespan of the piston and the engine itself. Furthermore, a smooth surface finish helps to maintain a proper seal between the piston rings and the cylinder walls, preventing blow-by and ensuring optimal compression and combustion.
The surface finish of the piston is achieved through various machining processes, such as honing and polishing. These processes create a smooth and uniform surface that minimizes friction and wear. The roughness of the surface finish is measured in microns (m) and is typically specified within tight tolerances to ensure optimal performance and longevity.
Optimizing the surface finish is an essential aspect of the piston crafting recipe. It contributes to improved engine performance, reduced emissions, and increased fuel efficiency. By minimizing friction and wear, a smooth surface finish enhances the overall durability and reliability of the piston, ensuring its effective operation throughout the engine’s lifespan.
Quality Control
In the context of piston crafting, quality control measures are paramount to ensuring the reliability, performance, and longevity of the final product. Rigorous quality control processes guarantee that each piston adheres to the precise specifications outlined in the piston crafting recipe, ensuring optimal engine operation.
- Dimensional Inspection: Each piston undergoes thorough dimensional inspection to verify its conformance to the design specifications. This includes measuring critical dimensions such as piston diameter, ring groove widths, and crown height. Any deviation from the specified tolerances can impact the piston’s fit and function within the engine.
- Surface Analysis: The piston’s surface finish is meticulously examined to ensure it meets the required smoothness and roughness specifications. A smooth surface finish reduces friction and wear, extending the piston’s lifespan and enhancing its sealing capabilities.
- Material Testing: The material used to craft the piston is subjected to rigorous testing to verify its strength, durability, and thermal properties. These tests ensure that the piston can withstand the extreme conditions encountered within the engine, including high temperatures, pressures, and mechanical stresses.
- Functional Testing: In some cases, pistons may undergo functional testing to assess their performance under simulated engine operating conditions. This testing helps identify any potential issues or defects that may not be apparent during static inspection.
By implementing stringent quality control measures throughout the piston crafting process, manufacturers can ensure that each piston meets the highest standards of quality and precision. This attention to detail contributes to the overall reliability and performance of the engine, maximizing its efficiency, power output, and lifespan.
FAQs on Piston Crafting Recipes
This section addresses frequently asked questions regarding piston crafting recipes, providing clear and informative answers to common concerns or misconceptions.
Question 1: What is the significance of material selection in piston crafting?
Answer: Material selection plays a critical role in determining the durability, performance, and reliability of the piston. The chosen material must possess the necessary strength, thermal conductivity, and wear resistance to withstand the extreme conditions encountered within the engine.
Question 2: How does machining accuracy impact piston performance?
Answer: Precise machining ensures proper fit and movement of the piston within the engine’s cylinder. It minimizes blow-by, reduces friction, and optimizes the piston’s performance and efficiency.
Question 3: What is the role of crown design in piston crafting?
Answer: The shape of the piston’s crown influences the combustion chamber shape, compression ratio, and air-fuel mixture movement. Optimizing the crown design enhances combustion efficiency, increases power output, and reduces emissions.
Question 4: Why is ring groove placement crucial in piston crafting?
Answer: Proper placement of ring grooves ensures effective sealing and oil control. The top ring prevents combustion gases from leaking past the piston, while the lower rings scrape excess oil from the cylinder walls. Precise groove placement optimizes engine performance and reduces emissions.
Question 5: How does surface finish affect piston longevity?
Answer: A smooth surface finish reduces friction and wear between the piston and cylinder bore. It extends the lifespan of the piston and improves engine efficiency by minimizing power loss.
Question 6: What are the key quality control measures implemented in piston crafting?
Answer: Rigorous quality control measures, including dimensional inspection, surface analysis, material testing, and functional testing, ensure that each piston meets the required specifications. These measures guarantee the reliability, performance, and longevity of the final product.
These FAQs provide a comprehensive overview of the key considerations and processes involved in piston crafting recipes. By addressing common questions, this section aims to enhance understanding and dispel any misconceptions.
Moving forward, the article will delve deeper into the technical aspects of piston crafting recipes, exploring material properties, machining techniques, and quality control methodologies.
Tips for Optimizing Piston Crafting Recipes
Crafting a high-performance piston requires careful consideration of material selection, machining accuracy, and quality control. Here are several tips to optimize the piston crafting recipe for enhanced engine performance and durability:
Tip 1: Select the Optimal Material
The choice of material significantly impacts the piston’s durability and performance. Consider factors such as strength, thermal conductivity, and wear resistance. Aluminum alloys offer a good balance of these properties, while steel provides superior strength for high-performance applications.
Tip 2: Ensure Precise Machining
Precise machining is crucial for proper piston fit and movement within the cylinder. Utilize computer-controlled machines to achieve tight tolerances and minimize blow-by. A well-machined piston reduces friction, enhances sealing, and optimizes engine efficiency.
Tip 3: Optimize Crown Design
The piston’s crown shape influences combustion efficiency and power output. Carefully design the combustion chamber shape, compression ratio, and valve pockets to promote efficient air-fuel mixing, complete combustion, and minimize heat transfer.
Tip 4: Place Ring Grooves Accurately
Proper ring groove placement is essential for effective sealing and oil control. Calculate the depth and spacing of the grooves precisely to ensure optimal ring pressure against the cylinder walls. This prevents blow-by, reduces friction, and maintains proper lubrication.
Tip 5: Achieve a Smooth Surface Finish
A smooth surface finish on the piston skirt and ring lands minimizes friction and wear. Utilize honing and polishing processes to achieve the desired surface roughness. This extends piston longevity, improves sealing capabilities, and enhances overall engine performance.
Tip 6: Implement Rigorous Quality Control
Establish comprehensive quality control measures throughout the piston crafting process. Conduct dimensional inspections, surface analysis, material testing, and functional testing to verify that each piston meets the specified tolerances. This ensures consistency, reliability, and optimal engine operation.
Summary
By following these tips and adhering to the piston crafting recipe, engineers can optimize piston design and manufacturing for improved engine performance, efficiency, and durability. These strategies contribute to the development of high-quality pistons that meet the demands of modern engines.
Conclusion
The piston crafting recipe is a critical element in the design and manufacturing of high-performance pistons. By carefully selecting materials, ensuring machining accuracy, optimizing crown design, placing ring grooves precisely, achieving a smooth surface finish, and implementing rigorous quality control, engineers can create pistons that meet the demands of modern engines.
Adhering to the piston crafting recipe contributes to improved engine performance, efficiency, and durability. These strategies ensure that pistons can withstand the extreme conditions encountered within the engine, minimize friction and wear, and optimize combustion and sealing. As engine technology continues to advance, the piston crafting recipe will remain a fundamental aspect of developing high-quality pistons that meet the challenges of the future.
Youtube Video:
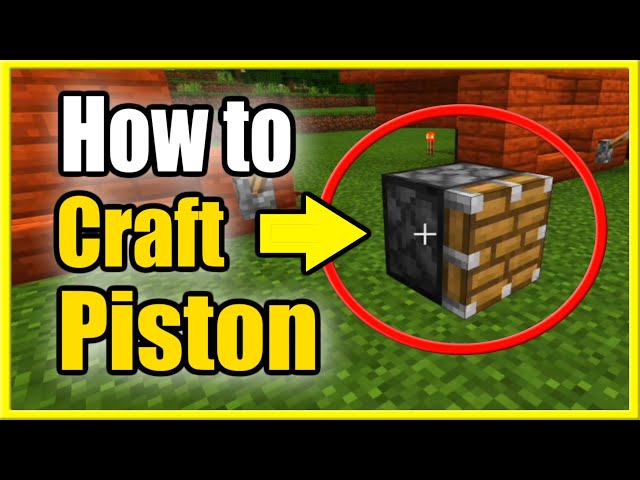