Crafting a heavy core involves manipulating and shaping the innermost part of a material to achieve a higher density and enhanced properties. Heavy cores are often employed in applications demanding strength, stability, and resistance to external forces. They are commonly found in industries such as construction, engineering, and manufacturing.
The significance of heavy cores lies in their ability to withstand significant loads, improve structural integrity, and enhance overall durability. By increasing the density of the core, it becomes more resistant to bending, compression, and other forms of deformation. This makes heavy cores ideal for use in load-bearing structures, foundations, and components that require exceptional strength.
Crafting heavy cores requires specialized techniques and materials. Common methods include using high-density materials, employing reinforcement techniques, and applying specialized treatments to increase the core’s density. By carefully controlling the composition and structure of the core, manufacturers can tailor its properties to meet specific performance requirements.
Crafting Heavy Cores
Crafting heavy cores involves manipulating the innermost part of a material to achieve a higher density and enhanced properties. The process encompasses various key aspects, each contributing to the overall quality and performance of the heavy core.
- Material Selection: Choosing materials with high density and strength.
- Core Design: Optimizing the shape and structure of the core for maximum density.
- Reinforcement Techniques: Employing reinforcements to enhance the core’s strength and stability.
- Density Control: Carefully controlling the density of the core to meet specific requirements.
- Treatment and Finishing: Applying specialized treatments to increase density and improve surface properties.
- Quality Assurance: Implementing rigorous quality control measures to ensure the core meets specifications.
- Testing and Evaluation: Conducting thorough testing to assess the core’s performance and properties.
- Applications and Performance: Understanding the specific applications and performance requirements for the heavy core.
These aspects are interconnected and play a crucial role in crafting high-quality heavy cores. By carefully considering each aspect, manufacturers can create heavy cores that meet the demands of various industries and applications. Heavy cores are essential components in structures, machinery, and equipment, providing strength, stability, and durability in demanding environments.
Material Selection
In the context of crafting heavy cores, material selection plays a pivotal role in determining the overall density and strength of the final product. Materials with high density and strength are essential for creating heavy cores that can withstand significant loads and external forces.
- High-Density Metals: Metals such as steel, iron, and lead possess high density and strength, making them suitable for crafting heavy cores in load-bearing structures, engineering components, and protective barriers.
- Composite Materials: Composites combining high-density materials with reinforcing fibers, such as carbon fiber or fiberglass, offer a unique blend of strength and lightweight properties, making them ideal for heavy cores in aerospace, automotive, and marine applications.
- Ceramics and Hard Materials: Ceramics like tungsten carbide and zirconia exhibit exceptional hardness and density, making them suitable for heavy cores in cutting tools, wear-resistant components, and armor.
- Specialized Alloys: Advanced alloys engineered for high density and strength, such as titanium alloys and shape-memory alloys, are used in critical applications where exceptional performance is required.
Choosing the appropriate material for a heavy core depends on the specific requirements of the application, including load capacity, strength-to-weight ratio, durability, and cost. By carefully selecting materials with high density and strength, manufacturers can create heavy cores that meet the demands of various industries and applications.
Core Design
In the context of crafting heavy cores, core design plays a critical role in achieving maximum density and optimizing the core’s performance. The shape and structure of the core directly influence its ability to withstand loads, resist deformation, and maintain stability.
- Shape Optimization: The shape of the core can be tailored to specific load requirements. For instance, a honeycomb structure can distribute loads evenly, while a ribbed structure provides additional support against bending.
- Structural Reinforcement: Internal ribs, trusses, and other structural elements can be incorporated into the core to enhance its strength and rigidity. These reinforcements help prevent buckling and collapse under heavy loads.
- Density Control: The density of the core can be controlled by varying the thickness of the core material and the spacing between structural elements. This allows manufacturers to fine-tune the core’s density to meet specific requirements.
- Material Compatibility: The core’s design must consider the compatibility of materials used. Different materials have different properties, and their combination should ensure optimal density and structural integrity.
By optimizing the core’s design, manufacturers can create heavy cores that are lightweight yet strong, capable of withstanding significant loads and external forces. Core design is an integral aspect of crafting heavy cores that meet the demands of various applications, from construction and engineering to transportation and manufacturing.
Reinforcement Techniques
In the context of crafting heavy cores, reinforcement techniques are crucial for enhancing the core’s strength and stability. Reinforcements are additional materials or structural elements introduced into the core to improve its load-bearing capacity and resistance to deformation. By employing reinforcement techniques, manufacturers can create heavy cores that can withstand significant external forces and maintain their structural integrity.
The choice of reinforcement technique depends on the specific requirements of the application. Common reinforcement techniques include:
- Fiber Reinforcement: Incorporating high-strength fibers, such as carbon fiber or fiberglass, into the core material. This technique enhances the core’s tensile strength and toughness.
- Truss Reinforcement: Adding truss structures within the core to provide additional support and prevent buckling. Trusses are lightweight and efficient in distributing loads.
- Ribbing: Creating ribs or webs within the core to increase its rigidity and resistance to bending. Ribs provide structural support and help maintain the core’s shape under load.
Reinforcement techniques play a vital role in crafting heavy cores that meet the demands of various applications. By understanding the connection between reinforcement techniques and the overall quality of heavy cores, manufacturers can optimize their designs to achieve the desired strength, stability, and durability.
Density Control
In the context of crafting heavy cores, density control plays a critical role in achieving the desired strength, weight, and performance characteristics. Density control involves carefully manipulating the core’s composition and structure to achieve a specific density that meets the requirements of the intended application.
- Material Selection: The choice of materials used in the core directly influences its density. High-density materials, such as metals and certain composites, contribute to a heavier core, while lightweight materials, such as foams and honeycomb structures, result in a lighter core.
- Core Design: The design and geometry of the core also affect its density. A solid core will have a higher density than a hollow core or a core with internal cavities. Engineers can optimize the core’s shape and structure to achieve the desired density while maintaining structural integrity.
- Manufacturing Process: The manufacturing process can also impact the core’s density. Techniques such as compaction, rolling, and sintering can be used to increase the density of the core material, while processes like foaming and molding can create cores with lower densities.
- Quality Control: Rigorous quality control measures are essential to ensure that the core meets the specified density requirements. Non-destructive testing methods, such as X-ray and ultrasonic testing, can be used to verify the core’s density and identify any defects or inconsistencies.
By carefully controlling the density of the core, manufacturers can create heavy cores that meet the specific demands of various applications. From load-bearing structures in construction to high-performance components in aerospace, density control is a crucial aspect of crafting heavy cores that are both strong and lightweight.
Treatment and Finishing
In the context of crafting heavy cores, treatment and finishing processes play a vital role in enhancing the core’s density and surface properties. These specialized treatments involve various techniques and materials to modify the core’s characteristics and optimize its performance.
- Surface Treatments: Surface treatments can be applied to increase the core’s density and improve its resistance to wear and corrosion. Techniques such as anodizing, plating, and thermal spraying can create a protective layer on the core’s surface, enhancing its durability and longevity.
- Impregnation: Impregnation involves infusing the core with resins, polymers, or other materials to fill pores and increase its density. This process enhances the core’s strength, stiffness, and resistance to moisture and chemicals.
- Heat Treatment: Heat treatment processes, such as annealing and tempering, can modify the core’s microstructure and improve its mechanical properties. Heat treatment can increase the core’s strength, hardness, and toughness, making it more resistant to deformation and failure.
- Coating: Applying protective coatings to the core’s surface can enhance its resistance to wear, corrosion, and environmental factors. Coatings can also provide electrical insulation and improve the core’s thermal properties.
By carefully selecting and applying appropriate treatment and finishing processes, manufacturers can create heavy cores with tailored properties that meet the specific requirements of various applications. These treatments enhance the core’s density, durability, and performance, ensuring that it can withstand the demands of demanding environments and applications.
Quality Assurance
Quality assurance is an essential aspect of crafting heavy cores, as it ensures that the final product meets the desired specifications and performs as intended. Rigorous quality control measures are implemented at various stages of the manufacturing process to verify the core’s dimensions, density, strength, and other critical properties.
- Inspection and Testing: Cores undergo thorough inspections and testing to assess their structural integrity, surface quality, and performance characteristics. Non-destructive testing techniques, such as ultrasonic and radiographic testing, are employed to identify any defects or imperfections.
- Material Traceability: Maintaining traceability of materials used in the core’s construction is crucial for quality assurance. This allows manufacturers to track the origin and properties of the materials, ensuring that they meet the required standards.
- Process Control: Establishing and adhering to standardized manufacturing processes helps ensure consistency and quality in the production of heavy cores. Process control measures include monitoring temperature, pressure, and other process parameters.
- Documentation and Records: Comprehensive documentation and record-keeping are essential for quality assurance. Manufacturers maintain detailed records of all inspections, tests, and process parameters to demonstrate the core’s compliance with specifications.
By implementing rigorous quality assurance measures, manufacturers can deliver heavy cores that meet the highest standards of quality and performance. These measures provide confidence that the cores can withstand the demands of demanding applications, ensuring safety, reliability, and longevity.
Testing and Evaluation
Testing and evaluation are crucial steps in the process of crafting heavy cores, as they provide objective data and insights into the core’s performance and properties. By conducting rigorous testing, manufacturers can ensure that the core meets the design specifications and is suitable for its intended applications.
- Performance Testing: Cores are subjected to various performance tests to assess their strength, stiffness, and durability. These tests simulate real-world conditions and loads to evaluate the core’s ability to withstand external forces and maintain its structural integrity.
- Material Characterization: Testing methods such as tensile testing, hardness testing, and microscopy are employed to characterize the core’s material properties. This data provides insights into the core’s composition, microstructure, and mechanical behavior.
- Non-Destructive Evaluation: Non-destructive testing techniques, such as ultrasonic testing and radiography, are used to assess the core’s internal structure and identify any defects or imperfections. These tests ensure that the core is free from cracks, voids, or other anomalies that could compromise its performance.
- Quality Control: Testing and evaluation play a vital role in quality control by verifying that the core meets the specified requirements. Manufacturers establish acceptance criteria based on testing results to ensure that only high-quality cores are released for use.
The data and insights obtained from testing and evaluation are essential for optimizing the core’s design, selecting appropriate materials, and implementing effective manufacturing processes. By thoroughly testing and evaluating heavy cores, manufacturers can ensure their reliability, safety, and suitability for a wide range of applications.
Applications and Performance
The connection between “Applications and Performance” and “how to craft heavy core” is critical because it drives the design, material selection, and manufacturing processes involved in crafting a heavy core. Understanding the specific applications and performance requirements provides valuable insights into the core’s intended use, enabling manufacturers to optimize its properties and ensure it meets the demands of the application.
For instance, in the construction industry, heavy cores are used in load-bearing structures, bridges, and high-rise buildings. These applications require cores with high strength, stiffness, and durability to withstand significant loads and external forces. By understanding the performance requirements for these applications, manufacturers can select appropriate materials, such as high-strength steel or reinforced concrete, and employ design techniques that enhance the core’s load-bearing capacity.
In contrast, heavy cores used in aerospace applications, such as aircraft and spacecraft, have different performance requirements. These cores must be lightweight yet strong to minimize the overall weight of the vehicle while maintaining structural integrity. Manufacturers achieve this by using advanced materials like carbon fiber composites and employing innovative core designs that optimize strength-to-weight ratios.
Understanding the specific applications and performance requirements for heavy cores is essential for crafting cores that are fit for purpose. It ensures that the core meets the necessary mechanical properties, durability, and weight constraints, enabling optimal performance in the intended application. By considering “Applications and Performance” as a crucial component of “how to craft heavy core,” manufacturers can create high-quality cores that meet the demands of diverse industries and applications.
Frequently Asked Questions
This section addresses common questions and misconceptions regarding the process of crafting heavy cores.
Question 1: What factors influence the density of a heavy core?
The density of a heavy core is primarily determined by the materials used, the core design, and the manufacturing processes employed. High-density materials, optimized core structures, and specialized techniques contribute to achieving the desired density.
Question 2: How is the strength of a heavy core enhanced?
Core strength is enhanced through reinforcement techniques, such as fiber reinforcement, truss reinforcement, and ribbing. These techniques introduce additional support and resistance to deformation, improving the core’s ability to withstand loads and external forces.
Question 3: What are the key quality control measures implemented in heavy core crafting?
Rigorous quality control measures ensure that heavy cores meet specifications and perform as intended. These measures include inspections, testing, material traceability, process control, and comprehensive documentation.
Question 4: How are heavy cores tested and evaluated?
Testing and evaluation play a crucial role in assessing the performance and properties of heavy cores. Performance testing, material characterization, and non-destructive evaluation techniques provide valuable data on strength, stiffness, durability, and structural integrity.
Question 5: How does understanding the applications and performance requirements impact heavy core crafting?
Understanding the specific applications and performance requirements is essential for optimizing heavy core design and material selection. It ensures that the core meets the necessary mechanical properties, durability, and weight constraints for the intended application.
By addressing these common questions, we aim to provide a comprehensive understanding of the factors, techniques, and considerations involved in crafting heavy cores. These insights contribute to the development of high-quality heavy cores that meet the demands of diverse industries and applications.
Transition to the next article section: Understanding the applications and performance requirements is crucial for optimizing heavy core crafting. The following section will delve deeper into the considerations and design principles for specific applications.
Tips for Crafting Heavy Cores
Crafting heavy cores requires careful consideration of materials, design, and manufacturing techniques. Here are some valuable tips to optimize the process and achieve high-quality results.
Tip 1: Choose High-Density Materials
The selection of materials with high density forms the foundation for a heavy core. Metals like steel, iron, and lead offer excellent density and strength. Composite materials combining high-density materials with reinforcing fibers provide a balance of strength and lightweight properties.
Tip 2: Optimize Core Design
The core’s shape and structure significantly impact its density and performance. Honeycomb structures distribute loads evenly, while ribbed structures provide additional support against bending. Optimizing the core design involves tailoring it to specific load requirements and density targets.
Tip 3: Employ Reinforcement Techniques
Reinforcements enhance the core’s strength and stability. Techniques such as fiber reinforcement, truss reinforcement, and ribbing introduce additional support. These reinforcements prevent buckling and collapse under heavy loads, ensuring the core’s structural integrity.
Tip 4: Control Density Precisely
Precise density control is crucial for achieving the desired performance. By carefully selecting materials, optimizing the core design, and employing appropriate manufacturing techniques, manufacturers can fine-tune the core’s density to meet specific requirements.
Tip 5: Implement Rigorous Quality Control
Rigorous quality control measures ensure that heavy cores meet specifications and perform as intended. Inspections, testing, material traceability, and process control are essential to verify the core’s dimensions, density, strength, and other critical properties.
Tip 6: Understand Applications and Performance Requirements
Tailoring heavy cores to specific applications requires understanding their performance requirements. Load-bearing structures in construction demand high strength and durability, while aerospace applications prioritize lightweight and strength-to-weight ratios. Considering these factors guides the selection of materials and design.
Tip 7: Utilize Advanced Manufacturing Techniques
Advanced manufacturing techniques, such as powder metallurgy, vacuum casting, and 3D printing, offer new possibilities for crafting heavy cores. These techniques enable the production of complex geometries, precise dimensions, and enhanced material properties, pushing the boundaries of heavy core capabilities.
Tip 8: Collaborate with Industry Experts
Collaborating with industry experts, such as material scientists, engineers, and manufacturers, can provide valuable insights and best practices for crafting heavy cores. Their expertise helps optimize designs, select appropriate materials, and implement effective manufacturing processes.
By following these tips and leveraging the latest advancements, manufacturers can craft high-quality heavy cores that meet the demanding requirements of various industries and applications.
Conclusion
In this comprehensive exploration of “how to craft heavy core,” we have delved into the intricacies of creating high-density cores for demanding applications. From material selection and core design to reinforcement techniques and quality control measures, we have emphasized the critical aspects that contribute to the performance and reliability of heavy cores.
Understanding the connection between “Applications and Performance” is paramount, as it drives the optimization of heavy core properties to meet specific requirements. Whether for load-bearing structures or lightweight aerospace components, tailoring the core’s design and material selection is essential for ensuring optimal performance.
As technology continues to advance, new materials and manufacturing techniques emerge, pushing the boundaries of heavy core capabilities. By embracing innovation and collaborating with industry experts, manufacturers can develop innovative solutions that meet the evolving demands of diverse industries. The future of heavy core crafting holds exciting possibilities, enabling the creation of even more robust, efficient, and versatile cores for a wide range of applications.
Youtube Video:
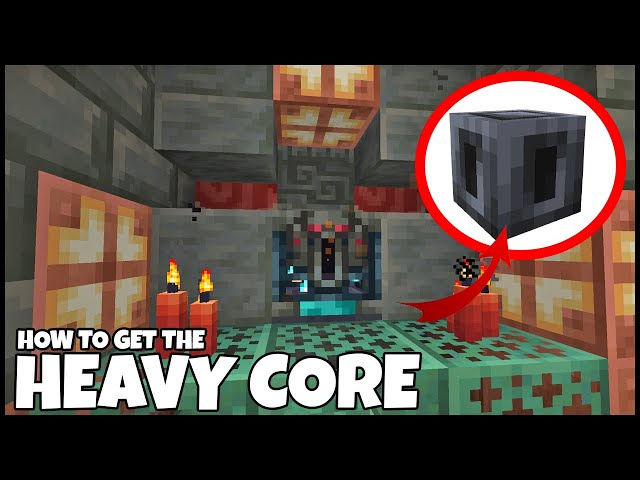