Crafting a lrail involves the meticulous assembly of a specialized type of extended rail system, often utilized in industrial or heavy-duty applications. This process demands precision and expertise to ensure the lrail’s structural integrity and operational efficiency.
Lrails play a pivotal role in various industries, facilitating the smooth and efficient movement of heavy loads across diverse terrains. Their robust construction and ability to withstand demanding conditions make them ideal for applications such as mining, manufacturing, and construction. Moreover, lrails offer exceptional durability and longevity, contributing to reduced maintenance costs and increased productivity.
To craft a lrail, several key steps must be meticulously executed. Firstly, the lrail’s design and specifications must be carefully planned to meet the specific requirements of the intended application. This includes determining the appropriate length, width, and weight-bearing capacity of the lrail. Subsequently, high-quality materials are selected, often involving durable metals such as steel or aluminum, to ensure the lrail’s resilience and longevity.
Crafting a Lrail
Crafting a lrail, an extended rail system designed for industrial applications, requires careful attention to several key aspects. These aspects, ranging from design considerations to material selection and construction techniques, play a crucial role in ensuring the lrail’s efficiency, durability, and safety.
- Design: The lrail’s design should consider factors such as length, width, and weight-bearing capacity to meet specific application requirements.
- Materials: High-quality materials, such as steel or aluminum, are essential for durability and longevity.
- Construction: Precise construction techniques, including welding and assembly, are critical for structural integrity.
- Alignment: Proper alignment of the lrail’s segments ensures smooth movement of heavy loads.
- Maintenance: Regular maintenance, including lubrication and inspection, is vital for optimal performance.
- Safety: Safety features, such as guardrails and warning signs, should be incorporated into the lrail’s design.
These key aspects are interconnected and interdependent. Careful consideration of each aspect during the planning and construction phases is essential to create a lrail that meets the intended purpose, ensuring efficient and safe operation for years to come.
Design
The design of a lrail is a critical aspect of crafting a lrail that meets specific application requirements. It directly influences the lrail’s functionality, efficiency, and safety. Factors such as length, width, and weight-bearing capacity must be carefully considered during the design phase to ensure the lrail can effectively handle the intended loads and operating conditions.
For instance, in a mining application where heavy machinery and materials need to be transported, a lrail with a robust design and sufficient weight-bearing capacity is essential. The length and width of the lrail should also be tailored to the specific layout of the mining site to facilitate efficient movement of loads.
In contrast, a lrail designed for a manufacturing facility might prioritize precision and accuracy over weight-bearing capacity. The length and width should be carefully calculated to ensure precise alignment and smooth movement of materials along the production line.
Therefore, understanding the specific application requirements is crucial for designing a lrail that is fit for purpose. By considering factors such as length, width, and weight-bearing capacity during the design phase, engineers can create a lrail that meets the unique demands of each application, ensuring optimal performance and safety.
Materials
In the context of crafting a lrail, the selection of high-quality materials is paramount for ensuring the lrail’s durability and longevity. The materials used in the construction of the lrail directly impact its ability to withstand demanding operating conditions and maintain its structural integrity over an extended period.
Steel and aluminum are two commonly used materials for lrails due to their exceptional strength-to-weight ratio, durability, and resistance to corrosion. Steel is known for its high tensile strength and load-bearing capacity, making it suitable for heavy-duty applications. Aluminum, on the other hand, offers a combination of strength and lightness, making it ideal for applications where weight reduction is a priority.
The use of high-quality materials in crafting a lrail is not only essential for ensuring its longevity but also for ensuring the safety and efficiency of the lrail system. Inferior materials may compromise the lrail’s structural integrity, leading to premature failure, increased maintenance costs, and potential safety hazards.
Therefore, careful consideration of material selection is a critical aspect of crafting a lrail. By choosing high-quality materials such as steel or aluminum, engineers and manufacturers can create lrails that are durable, long-lasting, and capable of meeting the demands of various industrial applications.
Construction
In the context of crafting a lrail, precise construction techniques are of paramount importance in ensuring the lrail’s structural integrity. This is because a lrail is subjected to demanding operating conditions, involving heavy loads and potentially harsh environments. To withstand these rigors, the lrail must be constructed with the utmost precision, employing techniques such as welding and assembly to create a robust and durable structure.
Welding, in particular, plays a vital role in joining the various components of the lrail, creating strong and reliable connections. The process of welding involves melting the metal components together, forming a permanent bond. This ensures that the lrail can the stresses and strains encountered during operation, preventing premature failure or structural damage.
Assembly, on the other hand, involves the meticulous fitting and joining of the lrail’s components to achieve proper alignment and functionality. This process requires skilled craftsmanship and attention to detail to ensure that the lrail operates smoothly and efficiently. Proper assembly also ensures that the lrail meets the required specifications and tolerances, guaranteeing its performance and safety.
Therefore, precise construction techniques, including welding and assembly, are indispensable components of crafting a lrail. By employing these techniques with the utmost care and precision, engineers and manufacturers can create lrails that are structurally sound, durable, and capable of meeting the demands of various industrial applications.
Alignment
In the context of crafting a lrail, proper alignment of its segments is a crucial aspect that directly affects the lrail’s functionality and efficiency. A lrail system is designed to handle heavy loads, and precise alignment of its segments is essential to ensure smooth movement of these loads along the rail’s length.
Misalignment of the lrail’s segments can lead to a variety of problems. Uneven distribution of weight along the rail can cause excessive stress on certain segments, potentially leading to premature wear and tear or even structural damage. Additionally, misalignment can result in increased friction between the load and the rail, hindering smooth movement and reducing the overall efficiency of the lrail system.
To achieve proper alignment, careful attention must be paid during the lrail’s construction phase. This involves ensuring that the individual segments are precisely fitted together and that the entire lrail is level and straight. Advanced surveying and alignment techniques are often employed to guarantee accuracy and precision throughout the alignment process.
Proper alignment of the lrail’s segments is not only essential for smooth movement of heavy loads but also contributes to the overall safety and reliability of the lrail system. A well-aligned lrail reduces the risk of derailments or accidents, ensuring the safe and efficient operation of the lrail for years to come.
Maintenance
Regular maintenance is an indispensable aspect of crafting a lrail that delivers optimal performance throughout its lifespan. By implementing a comprehensive maintenance program that encompasses lubrication and inspection, engineers and technicians can proactively address potential issues, minimize wear and tear, and ensure the lrail’s continued reliability and efficiency.
Lubrication plays a crucial role in reducing friction between the lrail’s moving components, such as wheels and bearings. Regular application of lubricants helps to maintain smooth movement, prevent excessive wear, and extend the lifespan of these components. Proper lubrication also minimizes energy consumption by reducing resistance, resulting in improved overall efficiency of the lrail system.
Inspection is equally important in identifying potential problems early on. Regular visual inspections can detect signs of wear, damage, or misalignment, allowing for timely repairs or adjustments. Advanced inspection techniques, such as ultrasonic testing or vibration analysis, can provide deeper insights into the lrail’s condition, enabling proactive maintenance and preventing catastrophic failures.
A well-maintained lrail not only operates more efficiently and reliably but also enhances safety. By promptly addressing maintenance needs, potential hazards are minimized, reducing the risk of accidents or derailments. Regular maintenance also helps to maintain the lrail’s structural integrity, ensuring that it can safely handle the intended loads and operating conditions.
In summary, regular maintenance, including lubrication and inspection, is an integral part of crafting a lrail that delivers optimal performance, reliability, and safety. By implementing a proactive maintenance program, engineers and technicians can extend the lifespan of the lrail, minimize downtime, and ensure its continued efficient operation.
Safety
In the context of crafting a lrail, incorporating safety features is paramount for ensuring the well-being of individuals operating or working near the lrail system. Safety features, such as guardrails and warning signs, play a critical role in preventing accidents, minimizing risks, and creating a safe working environment.
Guardrails, strategically placed along the lrail’s length, act as physical barriers to prevent falls or accidental contact with moving parts. They provide a sense of security, particularly in areas where personnel may be working close to the lrail’s path. Warning signs, prominently displayed at appropriate intervals, serve as visual cues to alert individuals of potential hazards, such as approaching vehicles or restricted areas.
The importance of incorporating safety features into the lrail’s design cannot be overstated. A well-designed lrail system should prioritize the safety of its users and minimize risks associated with its operation. By implementing these safety measures, accidents and injuries can be prevented, fostering a culture of safety and protecting human life.
FAQs about Crafting a Lrail
This section addresses frequently asked questions (FAQs) about crafting a lrail, providing concise and informative answers to common concerns and misconceptions.
Question 1: What is the purpose of a lrail?
A lrail is a specialized extended rail system designed for industrial applications. It facilitates the smooth and efficient movement of heavy loads across diverse terrains, commonly used in mining, manufacturing, and construction.
Question 2: What materials are commonly used to craft a lrail?
High-quality materials such as steel or aluminum are typically used for their durability and longevity. Steel offers high tensile strength and load-bearing capacity, while aluminum combines strength with lightness.
Question 3: How is the alignment of a lrail ensured?
Precise alignment is achieved through careful construction techniques and advanced surveying methods. Proper alignment ensures smooth movement of heavy loads, prevents excessive stress on the lrail, and enhances overall safety.
Question 4: Why is maintenance important for a lrail?
Regular maintenance, including lubrication and inspection, is crucial for optimal performance and safety. Lubrication reduces friction and wear, while inspection identifies potential issues early on, preventing breakdowns and ensuring continued reliability.
Question 5: What safety features should be incorporated into a lrail’s design?
Safety features such as guardrails and warning signs are essential to prevent accidents and protect individuals working near the lrail. Guardrails act as physical barriers, while warning signs alert of potential hazards.
Question 6: How does the design of a lrail impact its functionality?
The lrail’s design should consider factors like length, width, and weight-bearing capacity to meet specific application requirements. Proper design ensures efficient load handling, smooth movement, and optimal performance.
These FAQs provide a comprehensive overview of key considerations in crafting a lrail, emphasizing the importance of material selection, construction techniques, maintenance, safety, and design. Understanding these aspects is essential for creating a lrail that meets the demands of various industrial applications.
Transition to the next article section: Understanding the intricacies of crafting a lrail is crucial for its effective implementation and maintenance. The following section delves into the practical aspects of lrail construction, providing insights into the processes involved and best practices.
Crafting a Lrail
Crafting a lrail involves meticulous planning, careful construction, and diligent maintenance. To ensure the lrail’s longevity, efficiency, and safety, consider the following practical tips:
Tip 1: Precise Alignment
Properly align the lrail’s segments to ensure smooth movement of loads. Utilize surveying techniques and precision tools to achieve accurate alignment, minimizing friction and maximizing efficiency.
Tip 2: Durable Materials
Select high-quality materials such as steel or aluminum for exceptional strength and durability. These materials can withstand demanding operating conditions and heavy loads, ensuring the lrail’s long-term performance.
Tip 3: Regular Maintenance
Implement a regular maintenance program to maintain optimal lrail operation. Regularly lubricate moving parts to reduce wear and friction, and conduct inspections to identify and address potential issues, minimizing downtime and extending the lrail’s lifespan.
Tip 4: Safety Features
Incorporate safety features into the lrail’s design, such as guardrails and warning signs. These measures help prevent accidents by providing physical barriers and alerting personnel to potential hazards.
Tip 5: Skilled Workforce
Entrust the construction and maintenance of the lrail to a skilled and experienced workforce. Their expertise ensures adherence to best practices and industry standards, resulting in a safe and efficient lrail system.
Summary
By following these practical tips, engineers and technicians can craft lrails that meet the demands of various industrial applications. Precise alignment, durable materials, regular maintenance, safety features, and a skilled workforce are essential elements for constructing and maintaining a lrail system that delivers optimal performance, reliability, and longevity.
Transition to the article’s conclusion: The aforementioned tips serve as valuable guidelines for crafting a lrail that meets the highest standards of quality and functionality. As we conclude, it is important to emphasize the significance of ongoing monitoring and continuous improvement efforts to ensure the lrail’s continued effectiveness and safety.
Conclusion
In conclusion, crafting a lrail involves a comprehensive understanding of design principles, material selection, construction techniques, maintenance practices, and safety considerations. By adhering to best practices and utilizing the practical tips outlined in this article, engineers and technicians can create lrail systems that meet the demands of various industrial applications.
Ongoing monitoring and continuous improvement efforts are essential to maintain the lrail’s effectiveness and safety over its lifespan. Regular inspections, timely maintenance, and prompt repairs ensure the lrail continues to operate at its optimal capacity. A well-crafted and well-maintained lrail not only enhances productivity and efficiency but also contributes to a safe and reliable work environment.
Youtube Video:
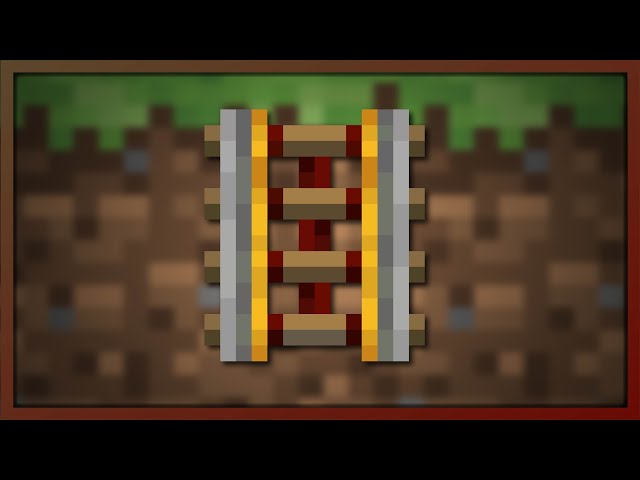